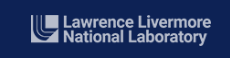
Lawrence Livermore National Laboratory (LLNL) and Verne, a San Francisco-based startup, have demonstrated a cryo-compressed hydrogen storage system of suitable scale for heavy-duty vehicles.
This is the first time cryo-compressed hydrogen storage has been demonstrated at a scale large enough to be useful for semi trucks, a milestone in high-density hydrogen storage.
Getting to net zero — reducing the nation’s annual output of greenhouse gases (GHGs) from 51 billion tons to zero — by 2050 will require a massive, accelerated deployment of alternative energy-efficient technologies across transportation, manufacturing, electricity, buildings and agriculture.
Transportation contributes the largest portion of total U.S. GHG emissions. Within the transportation sector, heavy-duty vehicles that rely on fossil fuels generate 23% of U.S. GHGs. Globally, trucks, ships and planes account for 10% of GHGs.
Energy-dense storage systems needed
Powering heavy-duty vehicles, such as Class 8 semi trucks, requires very energy-dense storage systems: even the most advanced batteries do not provide sufficient energy density. Hydrogen is a promising fuel source for these difficult-to-decarbonize sectors.
However, existing hydrogen-storage technologies do not provide diesel-parity performance, as these compressed-hydrogen storage systems have limited energy density capacity. Cryo-compressed (Cc) hydrogen, which can support the highest hydrogen densities in a compact storage system, can overcome this challenge.
Storing hydrogen in this state provides much greater energy density than other competing hydrogen platforms: relative to liquid, 700-bar compressed hydrogen at ambient temperature, and 350-bar compressed hydrogen at ambient temperature, CcH2 offers an improvement of 27%, 77% and 165% greater hydrogen density, respectively.
For the last two years, researchers at Livermore’s Cryogenic Hydrogen Fueling Facility with funding from Verne, have evaluated and tested Verne’s hydrogen-storage systems, successfully demonstrating a new advance in high-density hydrogen storage for heavy-duty vehicles.
“Past work at LLNL on cryo-compressed hydrogen storage has focused on the light-duty automotive sector. Storage systems for heavy-duty vehicles need to store an order of magnitude more hydrogen, greatly increasing the cost and time required for testing,” said Nick Killingsworth, principal investigator and mechanical engineer at the Laboratory.
The challenge of testing the technology highlights the importance of detailed, upfront test planning, complemented with advanced simulations, to establish efficient test programs, which embodies the collaborative work between LLNL and Verne.
Single-tank system tested
Recently, the LLNL and Verne teams tested a single-tank system, demonstrating storage of more than 29 kilograms of cryo-compressed hydrogen.
This benchmark is three times greater than what has been previously demonstrated with any single CcH2 storage system and roughly equivalent to a one-megawatt-hour battery system, yet in a lighter and more compact storage unit.
The system is compact enough that it can fit where diesel tanks are typically installed on a Class 8 truck: on the side of the truck between the wheels. In addition to a different tank design, the components and functionality were enhanced to handle this larger volume.
“Despite the promise from early hydrogen-fueled truck pilots, the efficient storage of hydrogen onboard trucks, ships and planes remains one of the main challenges to unlock a zero-emission future,” said David Jaramillo, co-founder of Verne.
“Verne has developed high-density, lightweight hydrogen storage systems for use onboard heavy-duty vehicles at low cost. Our solution builds upon decades of research pioneered at Livermore to provide a reliable, scalable and cost-effective storage solution. We could not have done this without the team at Livermore. It’s exciting to see this project head toward the commercialization phase where it can be adopted across the heavy-duty sector.”
The Laboratory’s testing facility and safety-review process have provided Verne with access to unique equipment and expertise typically unavailable to a startup that has not had time to build up infrastructure and safety processes. This access has allowed Verne to quickly assess the performance of its cryo-compressed-hydrogen storage systems.
More than 25 years ago, Salvador Aceves, then a mechanical engineer at LLNL, demonstrated through thermodynamic modeling the benefits of CcH2. He then led a team at LLNL that designed and built three generations of tanks, including a CcH2 tank that was used to drive more than 650 miles in a modified passenger vehicle on a single tank of hydrogen.
“It is great to see all our work on cryo-compressed hydrogen storage systems over the years is on a path to reduce carbon emissions in the heavy-duty transportation sector,” said Francisco Espinosa-Loza, a group leader at LLNL and part of the team that built all three generations of LLNL’s CcH2 tanks.
Lab has novel hydrogen refueling system
LLNL also is the site of a novel hydrogen refueling system built to directly pressurize liquid hydrogen storage systems capable of reaching higher densities than the starting liquid.
The work performed by LLNL was primarily sponsored by the Hydrogen and Fuel Cell Technologies Office within the Department of Energy’s Office of Energy Efficiency and Renewable Energy.
In 2021, Verne was selected as one of Breakthrough Energy’s (BE) inaugural fellows projects, a program that backs early-stage climate ideas with funding and support to accelerate the path from innovation to commercialization. Most of the engineering and testing for this demonstration was funded and supported by the BE’s Fellows Program.
“Developing and scaling a novel climate technology takes a robust network of complementary partners. The Breakthrough Energy Fellows Program is proud to support Verne as part of an ecosystem that includes national labs like LLNL, industry partners, and other sources of patient capital. It’s incredible to see the technical progress that the Verne team has achieved during their time in the Breakthrough Energy Fellows program and in partnership with LLNL,” said Ashley Grosh, vice president of the Fellows Program at Breakthrough Energy, an organization founded in 2015 to accelerate innovation in sustainable energy and other technologies to reduce greenhouse-gas emissions.
Amazon, through its Climate Pledge Fund, is an early investor in Verne.
“Verne addresses two of the critical limitations of hydrogen to power heavy-duty transport: density and cost. Amazon is excited to see Verne achieve a major technical milestone and demonstrate record hydrogen-storage density. This work, enabled by funding from Amazon’s Climate Pledge Fund and LLNL’s world-class facilities and team, takes Verne a step closer to meeting the zero-emission transport requirements of future customers like Amazon,” said Matt Peterson, director of Amazon’s Climate Pledge Fund.
IMAGE (above): IMAGE (above): Picture of the researchers standing next to Verne’s cryo-compressed hydrogen storage system, with LLNL’s cryogenic hydrogen fueling facility in the background. From left to right: Kara Zhang, a Verne process engineer; LLNL mechanical engineer Nick Killingsworth; Ted McKlveen, Bav Roy and David Jaramillo, all co-founders of Verne; and Verne mechanical engineer Harry Clarke. Credit: LLNL.